Ниже приведен подробный ответ на вопрос о конфигурации камнедробильного оборудования мощностью 500-600 т/час с конусной дробилкой:
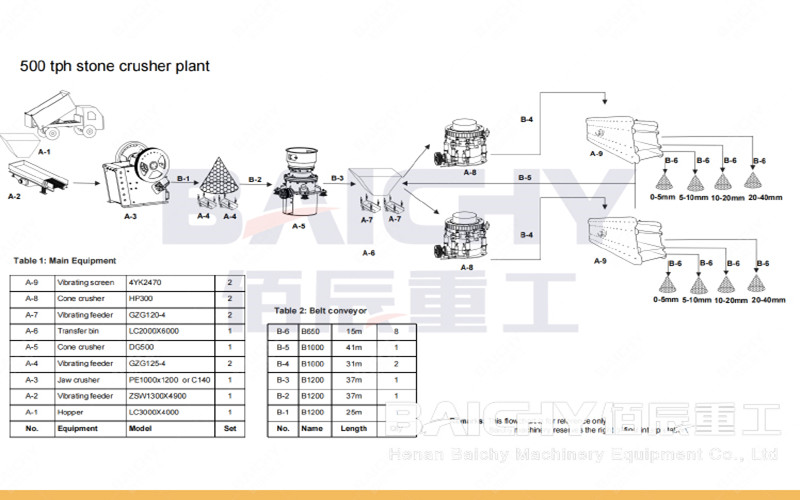
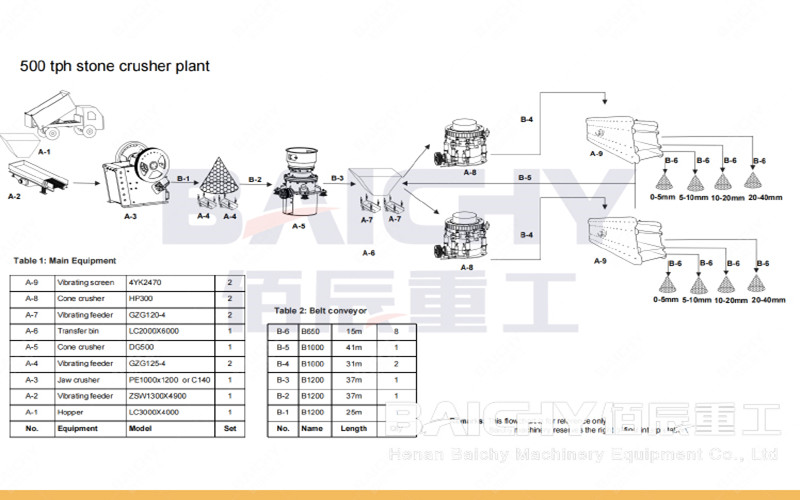
Обзор камнедробильного оборудования мощностью 500-600 т/час.
Камнедробильное оборудование в основном используется для измельчения крупных кусков камня до требуемых размеров частиц и широко используется в строительстве, на автомобильных и железных дорогах, в охране водных ресурсов и других областях. При производственной мощности в 500-600 тонн в час конфигурация конусной дробилки может обеспечить эффективный и стабильный эффект дробления.
Конфигурация камнедробильного оборудования мощностью 500-600 тонн в час.
1. Тип: многоцилиндровая гидравлическая конусная дробилка (например, HPM500)
2. Производственная мощность: В зависимости от типа полости конусной дробилки, производительность может достигать 365-790 тонн в час, что соответствует производственным потребностям в 500-600 тонн в час.
3. Тип дробильной полости: доступны различные типы полостей, которые можно адаптировать для операций дробления с различными требованиями к размеру частиц.
4. Мощность двигателя: обычно он оснащен двигателем мощностью около 400 кВт, обеспечивающим высокую мощность дробления.
5. Конструктивные особенности: Изготовлен из стали с высоким содержанием марганца, износостойкой и коррозионностойкой; с гидравлической регулировкой разгрузочного отверстия, защитой от перегрузки и другими функциями.
Вспомогательное оборудование для камнедробильного оборудования мощностью 500-600 тонн в час.
1. Вибрационный питатель: используется для равномерной и непрерывной подачи измельчаемого камня в конусную дробилку.
2. Щековая дробилка (опционально): как основное дробильное оборудование, она выполняет предварительное дробление крупных кусков камня для уменьшения размера частиц и облегчения последующей обработки в конусной дробилке.
3. Вибрационный грохот: используется для просеивания щебня и отделения частиц, соответствующих требованиям.
4. Ленточный конвейер: используется для транспортировки щебня от конусной дробилки к вибрационному грохоту или другому оборудованию.
Принцип работы камнедробильного оборудования мощностью 500-600 т/ч (тонн в час)
Принцип работы конусной дробилки заключается в приведении горизонтального вала во вращение с помощью двигателя, а горизонтальный вал приводит во вращение эксцентриковую втулку с помощью зубчатой передачи. Эксцентриковая втулка приводит в движение главный вал, заставляя подвижную коническую часть качаться, тем самым создавая периодическое относительное движение между эксцентрично качающейся подвижной конической облицовкой и неподвижной конической облицовкой. Измельчаемый материал поступает в дробилку из верхнего загрузочного отверстия, сжимается и деформируется в камере дробления и измельчается, а измельченный материал выгружается из разгрузочного отверстия в нижней части дробилки.
Преимущества камнедробильного оборудования производительностью 500-600 т/час
1. Высокая эффективность и стабильность: конусная дробилка использует передовые технологии дробления и конструктивное исполнение, обеспечивая высокую эффективность и стабильную производительность дробления.
2. Высокая адаптивность: доступны различные типы камер для адаптации к операциям дробления с различными требованиями к размеру частиц; в то же время, различное вспомогательное оборудование может быть сконфигурировано для формирования полной производственной линии дробления.
3. Энергосбережение и защита окружающей среды: гидравлическая регулировка разгрузочного отверстия, защита от перегрузки и другие функции используются для снижения энергопотребления и частоты отказов; в то же время снижается уровень шума и запыленности, что соответствует требованиям охраны окружающей среды.
4. Удобство обслуживания: оборудование имеет компактную конструкцию и простое управление; оно изготовлено из износостойких материалов для снижения затрат на износ и техническое обслуживание.
Выше приведено описание конфигурации камнедробильного оборудования мощностью 500-600 вт с конусной дробилкой. Конкретная конфигурация может быть скорректирована и оптимизирована в соответствии с фактическими производственными потребностями.